Productie
In Hendrik-Ido-Ambacht beschikt Bolidt over een moderne fabriek, met een state-of-the-art machinepark, dat voldoet aan de strengste milieunormen. Onze medewerkers zijn er bovendien op getraind om alle mogelijke verspilling van o.a. tijd, logistiek en materiaal te voorkomen, geheel volgens de LEAN filosofie.
Maximale efficiency in productie is het resultaat, waardoor de milieu-impact wordt geminimaliseerd.
Productie
In Hendrik-Ido-Ambacht beschikt Bolidt over een moderne fabriek, met een state-of-the-art machinepark, dat voldoet aan de strengste milieunormen. Onze medewerkers zijn er bovendien op getraind om alle mogelijke verspilling van o.a. tijd, logistiek en materiaal te voorkomen, geheel volgens de LEAN filosofie.
Maximale efficiency in productie is het resultaat, waardoor de milieu-impact wordt geminimaliseerd.
De strakke en efficiënte productieplanning die Bolidt hanteert, heeft tevens zijn weerslag op de inkoop van materiaal.
Wij zijn in staat just-in-time in stuks in te kopen, waardoor het aantal transporten wordt geminimaliseerd en waardoor er geen onnodige voorraad van grondstoffen nodig is. Bovendien werken we met een netwerk van eigen en externe transporteurs, waardoor we een hoogst efficiënte transportplanning kunnen hanteren.
Gevolg is dat de CO2-uitstoot voor de aanvoer van materialen beperkt is. Steeds modernere productieplanningen stellen Bolidt in staat zo efficiënt mogelijk te produceren, van wit naar zwart.
Door een zorgvuldige planning wordt ook het gebruik van schoonmaakmiddelen gereduceerd.
Met een zorgvuldige planning kunnen we eveneens het gebruik van schoonmaakmiddelen reduceren. Zo is de afgelopen jaren het acetonverbruik in de productie ten behoeve van het reinigen van mengapparatuur sterk gereduceerd. Oorzaak hiervan is onder andere de overgang naar kleinverpakkingen (van 200 ltr drums naar 20 ltr cans). Daarnaast wordt voor de 1e reiniging vervuilde aceton gebruikt en pas voor de 2e reiniging schone aceton. Alle vervuilde aceton wordt gerecycled (destillatie) en komt terug als nieuw reinigingsmiddel. In 2012 is Bolidt over gegaan op een milieuvriendelijker en gebruiksvriendelijker reinigingsmiddel dat ook regenereerbaar is. Hierdoor is vanaf 2012 het verbruik van aceton als reinigingsmiddel voor de productinstallaties gereduceerd tot vrijwel 0 ltr.
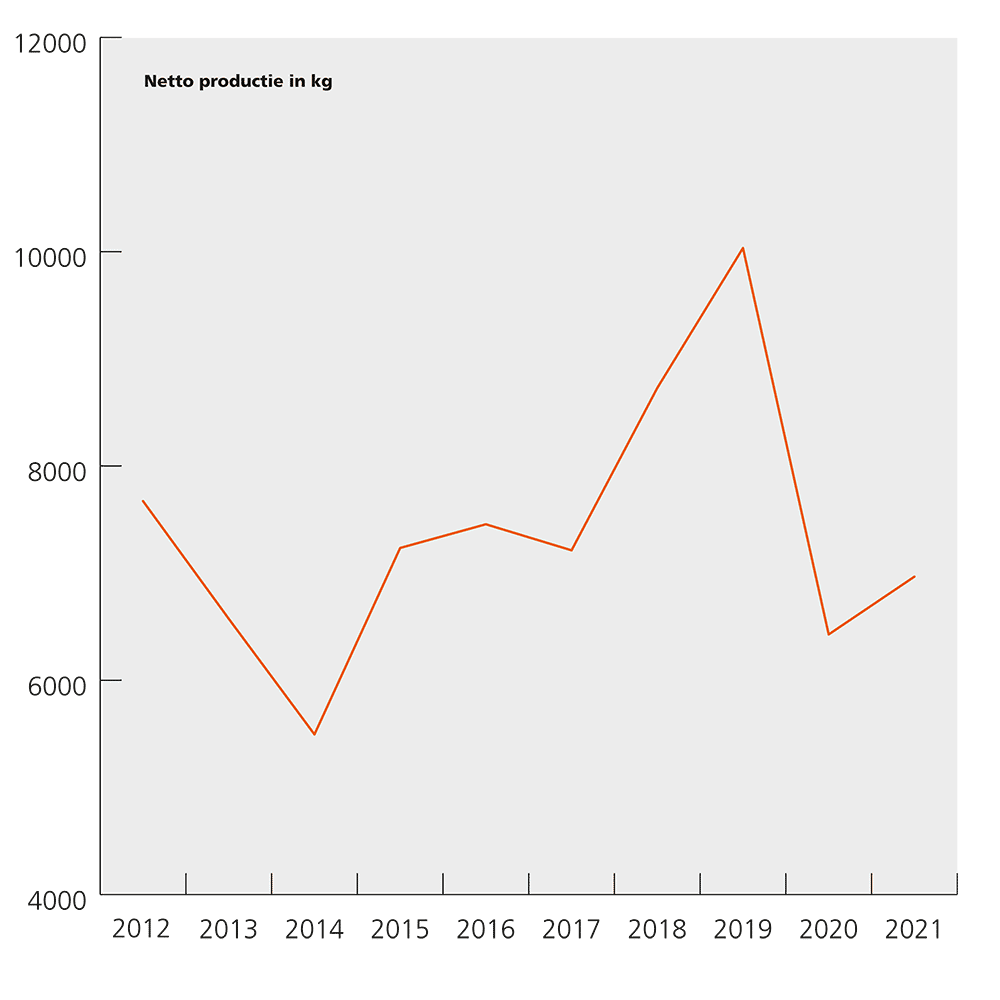
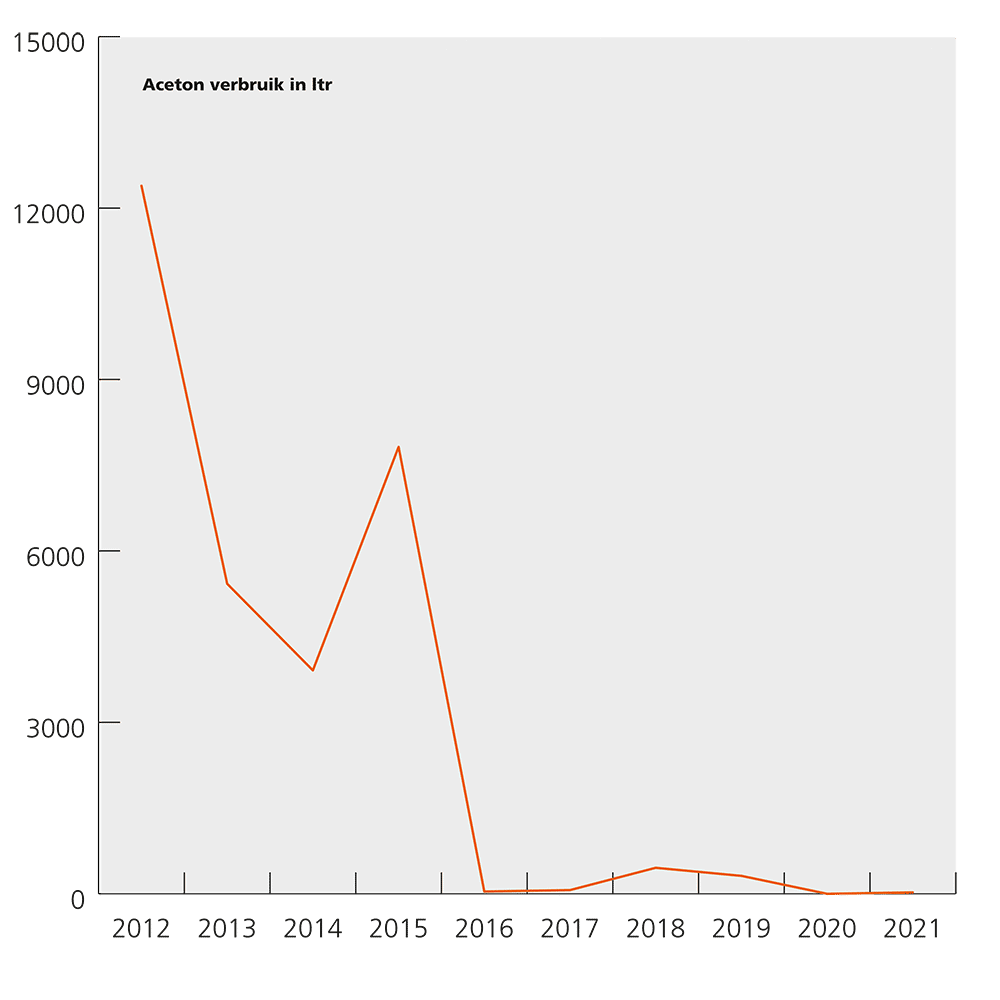